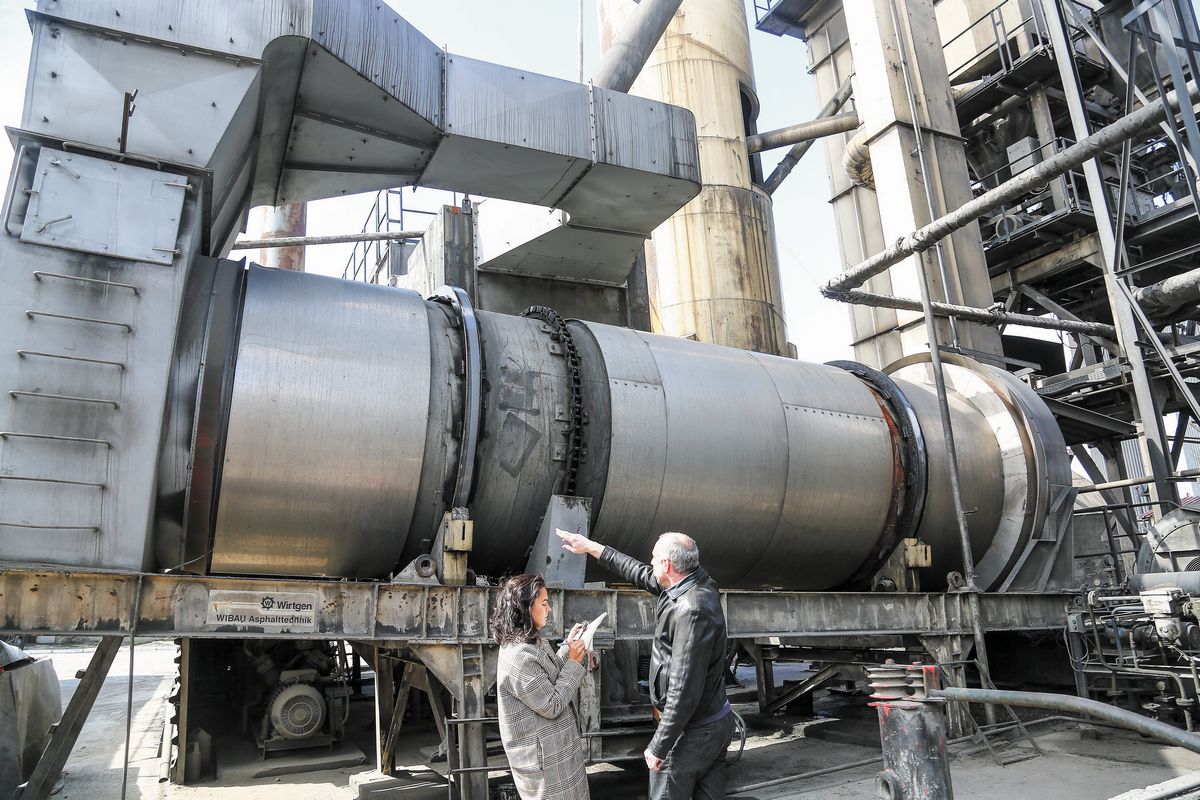
С началом ремонта дорог в городе репортерская группа «Иркутска» побывала на асфальтобетонном заводе и убедилась, какая это огромная и важная отрасль экономики — производство асфальта.
В этом году Иркутский асфальтобетонный завод «проснулся» 10 апреля — это самый ранний запуск за всю его историю. Зимой, когда нет дорожных работ, завод встает на ремонт: обновляется, меняет изношенные механизмы, готовится к новому сезону. А весной пробуждается, набирает обороты и к августу выходит на рекордные мощности — до 2000 тонн асфальтобетонной смеси в сутки. Если вы спросите, на что похож асфальтобетонный завод изнутри, мы, сотрудники редакции «Иркутска», ответим не задумываясь: «На большую кулинарную студию». За широким стеклом варщик на компьютере «замешивает» блюда из песка, щебня и битума по проверенным рецептам. Полученную смесь спешат раскатать по городским улицам, ведь асфальт живет лишь несколько часов. В это время в лаборатории женщина с ситом уже просеивает готовый продукт, «запекает» в печи и формирует из него «куличи». Что сказать — настоящая дорожная кухня!
СТРОГО ПО РЕЦЕПТУ
По утрам на предприятии оживает телефон и начинают сыпаться заявки. Их принимают день в день, потому что асфальт должен быть горячим, свежим.
— У нас продукция, которая долго не лежит. Мы можем подержать его своих бункерах-«термосах» максимум 2–3 часа. В погрузчиках створки кузова сделаны с подогревом, это не дает смеси застыть, — объясняет управляющий асфальтобетонным заводом МУП «ИркутскАвтодор» Алексей Севастьянов. — Каждый заказчик сообщает с утра, сколько нужно асфальта и какого типа. На тротуары идет асфальт типа В, на дороги пожестче: тип А, Б или смесь ЩМА (щебеночно-мастичный асфальтобетон. — Прим. авт.). По составу они отличаются количеством щебня и добавками. Например, для верхних слоев добавляется минеральный порошок — он увеличивает плотность и водостойкость. Для нижних слоев, наоборот, порошок не кладем, чтобы получился пористый асфальт. Смесь ЩМА отличается повышенным содержанием щебня: в обычном асфальте его 30–60 %, а в ЩМА не менее 70 %.
Все эти пропорции кропотливо высчитаны сотрудниками лаборатории и занесены компьютер в виде готовых рецептов. Оператор (он же варщик) выбирает номер рецепта, вводит нужный тоннаж, и шестеренки завода оживают.
ВЫСШИЙ ПИЛОТАЖ
Наверху в операторской за широким стеклом сидит мужчина с прекрасной фамилией Мужиков. Перед ним — огромная панель с кнопками и рычажками: «Пламя», «Рыхлитель», «Ковш», «Горелка», «Вяжущее». На них варщик разыгрывает очередную симфонию асфальта.
— Здесь сложнее, чем на самолете, механизмов больше, — смеется Валерий Мужиков. — Из-за ошибки варщика может заклинить барабан или элеватор, получится непригодный асфальт, а может и остановиться весь завод.
На экране у Валерия Мужикова отображаются бункеры, заполненные песком и щебнем. Он отмеряет нужное количество и одной кнопкой отправляет их в сушильный барабан, где начинает настоящая мясорубка. Внутри сушильного барабана инертные материалы проходят по спирали через факел температурой 500 °С.
— После этого просушенный материал по элеваторам поднимают на самый верх, на «грохот». Это такие сетки; пройдя через них, материал делится на несколько фракций и распределяется по четырем накопительным бункерам. Затем через весы подается в смеситель, по трубам туда же впрыскивается битум. И уже готовый асфальт поступает в бункеры. У нас их два по 50 тонн, так что можно хранить разные типы, — описывает производственный процесс Валерий Мужиков.
— Хороший асфальт получается?
— Самый лучший! — уверенно отвечает варщик.
— А почему его тогда приходится так часто менять?
— Многое зависит от основания. Во время ремонта меняют первый, максимум второй слой, а что там внизу — кто его знает. Вот улица Байкальская, например, стоит который год, ей мало что делается, потому что она была грамотно спроектирована, с учетом современных нагрузок, с хорошим водоотведением, — подхватывает разговор Алексей Севастьянов. — Именно вода разрушает асфальт. Под камушек забежит, несколько перепадов температуры с плюса на минус — и все, за неделю разорвет покрытие. Вот на Култукской сейчас сделали реконструкцию, основание поменяли, водоотведение сделали — она теперь должна долго простоять. В том году меняли дорогу на Чехова, тоже в основание положили хорошую «подушку».
В активную фазу дорожного ремонта завод работает круглосуточно. Например, сейчас идет ремонт 20-го Советского переулка, свежий асфальт подвозят непрерывно.
— Важно заранее рассчитать, сколько асфальта потребуется. Хорошо, если есть несколько заказчиков, кому-то не хватило — поделились, — продолжает Алексей Николаевич. — А не как сегодня: заказали на 20-й Советский 60 тонн, а потом позвонили и сказали, что еще 15 не хватает... Хорошо, завод горячий был!.. А вообще запускать производство меньше чем на 100 тонн асфальта невыгодно: чтобы разогреть завод, требуется полтонны солярки.
Важный заказчик в этом сезоне — международный аэропорт «Иркутск». Уже третий год «ИркутскАвтодор» частями ремонтирует там взлетно-
посадочную полосу и рулежные дорожки.
— Для «взлетки» мы используем битум на полимере. Специфика в том, что он должен постоянно находиться в движении, у нас есть две специальные емкости, оборудованные мешалками, — указывает на оборудование управляющий. — Процесс укладки строго выверен: сначала на взлетно-посадочную полосу приезжают дорожники, выставляют фрезу, она снимает асфальт. В это время нам доставляют полимерно-битумное вяжущее с Байкальского битумного терминала, мы должны его быстро замесить, приготовить асфальт и без промедления подать туда, на взлетно-посадочную. Все строго, ведь на время ремонта останавливают авиасообщение.
С каждой партии асфальта — неважно, идет он на дворовый тротуар или взлетно-посадочную полосу, — отбираются образцы для лаборатории. После этого в дело вступают химики.
КОМНАТА ПЫТОК ДЛЯ АСФАЛЬТА
Если все рецепты выверены и занесены в компьютер, то возникает резонный вопрос: зачем проверять каждую партию асфальта? По словам управляющего, это защищает от непредвиденных ситуаций: сбоя в программе, прорыва сетки на «грохоте», брака в поставляемых материалах.
— Пару лет назад, когда мы только начали производить ЩМА, попалась бракованная стабилизирующая добавка. Мы это не сразу поняли. Она оказалась переувлажненной, не сработала в асфальте, получился брак, — вспоминает Алексей Севастьянов.
К тому моменту, когда обнаружили дефект, на улице Ширямова уже успели закатать несколько десятков метров асфальта. Пришлось снимать покрытие и укладывать заново. Но такие случаи единичны. Как правило, сотрудники лаборатории могут визуально заметить отклонение от нормы еще на стадии производства и сразу же откорректировать рецепт.
— Если смесь получается сухой, видны зерна щебня — значит, недостаточно битума. Добавляем. Если видим, что асфальт «живой», плывет и растекается, то, наоборот, уменьшаем количество битума. В общем, визуальный осмотр никто не отменял, — рассказывает Гертруда Карпец, начальник лаборатории контроля качества асфальтобетонного завода МУП «ИркутскАвтодор». — А здесь, в нашей лаборатории, проводятся уже специфические испытания с образцами.
Первым делом отобранный асфальт высыпают в специальный металлический лоток, хорошо перемешивают и смотрят: выдержан ли зерновой состав? Затем помещают в муфельную печь и запекают при 500 °С, чтобы выгорел битум. Оставшуюся массу прогоняют сквозь сита и вновь оценивают зерновой состав по фракциям. Далее — формовка. С помощью пресса рыхлую массу превращают в аккуратный плотный цилиндр.
— На следующий день, после полного остывания образцов, начинаются испытания в воде, — поясняет Гертруда Ивановна. — Каждый пробник взвешивают в сухом состоянии и в воде. Затем мы помещаем образец в вакуум на час, выкачиваем весь воздух, возвращаем нормальное давление и опускаем асфальт в воду — она заполняет поры. Так мы проверяем водонасыщение.
«С ТАКОЙ ПОЭЗИЕЙ — О КАМЕНЮКАХ?!»
Первое, что бросается в глаза в лаборатории, — это «битумное дерево» на столе. Из металлического ствола растут скукожившиеся смоляные «листочки». Гертруда Ивановна любовно называет эту конструкцию листопадом:
— Испытания с адгезионными добавками — это же поэзия! Каждый «листочек» — результат того, как ведет себя битум с разными добавками. Когда кипятишь образцы в соляном растворе, с одного все стекает, а на другом битум задерживается, образуя вяжущую пленку. На основании этих испытаний мы потом выбираем поставщика добавок.
О своей работе Гертруда Карпец рассказывает так вдохновенно, будто вокруг нее не асфальт и битум, а как минимум полотна эпохи Возрождения.
— В 1999 году, как запустили завод, меня переманили сюда с Марковского асфальтобетонного завода. Вообще я училась в Политехе по специальности «Строительные технологии», нас больше учили работать с железобетоном, цементобетоном — там понятные реакции, свойства, прочность. А когда я пришла на асфальтовый завод, то задумалась: «А тут за счет чего можно улучшить свойства материала?» Постепенно начала раскрывать тонкости битумов, экспериментировать с добавками, выводить рецепты, оттачивать их — как любая хозяйка на кухне. Я женщина-таблица, женщина-технарь, поэтому мне все это интересно. Когда я начинаю в очередной раз восторженно рассказывать про свою работу, мне дочь говорит: «И что, с такой поэзией — о каменюках?»
Гертруда Ивановна говорит, что за 20 лет технология производства асфальта практически не изменились, а вот требования — значительно. Когда Иркутск вошел в национальный проект «Безопасные и качественные автомобильные дороги» и получил федеральное финансирование на ремонт улиц, проверки качества ужесточились. В прошлом году вдобавок изменились ГОСТы для асфальтобетонных смесей. У завода есть три года, чтобы перестроить свою работу, и первый важный шаг уже сделан: в коробках стоит новое оборудование, ждет своего часа. Это сушильный шкаф с циркуляцией воздуха, вакуумное оборудование с вибрацией для испытания асфальтобетонов, весы для гидростатического взвешивания образцов, новый испытательный пресс.
— Наш пресс формирует образцы методом двухстороннего сжатия, а новая установка — ударного типа, так называемый уплотнитель Маршалла. Он совершает определенное количество ударов, в результате спрессованный образец получается в виде шайбы, а не цилиндра, — объясняет Гертруда Ивановна. — К следующему году планируем запустить оборудование.
За сезон, который длится с апреля по ноябрь, иркутский асфальтобетонный завод успевает выпустить примерно 100 тысяч тонн асфальта и 1200 тонн битумной эмульсии. В зимнее время года варщики превращаются в сварщиков (чинят агрегаты и механизмы), а лаборатория совершенствует рецепты. В конце декабря наступает «зимняя спячка»: все сотрудники уходят в отпуск и возвращаются только в середине февраля. В марте на заводе начинается новый цикл.
Яна Шутова
Фото Валентина Карпова
На территории иркутского асфальтобетонного завода можно снимать технологические блокбастеры. Это царство огромных механизмов и сооружений, которыми управляет человек за компьютерным пультом. Завод в Иркутске смонтировали в 2000 году, оборудование тут немецкое, и оно постоянно обновляется. Городская власть считает завод стратегическим объектом для города: очень важно, что мы имеем свое производство асфальта, которое контролируем по качеству. Иркутский АБЗ полностью покрывает потребность города в асфальте, более того — его продукцию покупают строительные компании
Управляющий асфальтобетонным заводом Алексей Севастьянов рассказывает журналисту «Иркутска» Яне Шутовой, как песок и щебень, пройдя через «мясорубку» и 500-градусное пламя, смешиваются с битумом и превращаются в знакомый нам асфальт
Это мраморная крошка, ее поставляют из Слюдянки. Пару лет назад на асфальтобетонном заводе Иркутска установили мельницу, чтобы самим производить минеральный порошок. Его добавляют в верхние слои асфальта для водостойкости
Так проводятся испытания добавок для асфальта. Образцы окунают в разные растворы, потом высушивают и смотрят: если есть черный блеск, значит, битум держится — добавка хорошая! Если битум стекает с образца — добавка не пойдет
Человек, который знает про асфальт все! Начальник лаборатории асфальтобетонного завода Гертруда Карпец работает на предприятии со дня его основания — более 20 лет
Варщик асфальтобетонной смеси Валерий Мужиков — отличный профессионал и человек интересной судьбы! В начале 1990-х Валерий Валентинович работал в геологии на территории Монголии, затем проехал по всему миру: Турция, Венгрия, Югославия, Словения, Южная Корея, Китай. На несколько лет задержался в Италии, где открыл небольшой бизнес, а в 2014 году вернулся в Иркутск и пришел на асфальтобетонный завод
Так выглядят образцы асфальта, которые отбирают для проверки на качество в лаборатории АБЗ. От каждой партии асфальта, которую вывозят с завода, берут три пробы. Для этого на выезде с территории завода стоит лестница, а на ней лежит железная лопатка. Лаборант поднимается, зачерпывает из погрузчика образец и относит в лабораторию
В лаборатории АБЗ на батарее сушатся камни — обычные булыжники. Как выяснилось, потом они превращаются вот в таких пингвинчиков, черепашек и божьих коровок. Так сотрудники лаборатории отвлекаются от рутинной работы: во время обеда 10 минут тратят на трапезу, а потом берутся за кисточки